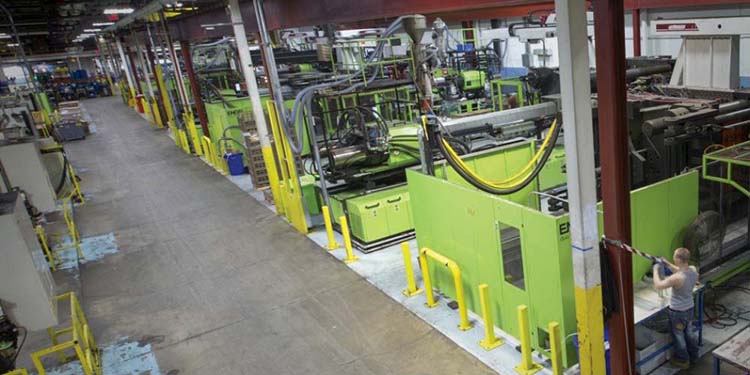
By: Flexxbotics, June 2021
Dynamic Automation with Peace of Mind:
Port Erie Case Study
Port Erie: A Rapidly Growing Injection Molding Company
Port Erie’s Plastics, an injection molding company located in Northwest Pennsylvania, has been growing rapidly over the past two decades. Situated in a hotbed of activity in the plastics industry, they have a manufacturing and warehousing complex that encompasses 615,000 square feet in four buildings with nearly 90 injection molding machines and about 400 full-time employees.
Port Erie’s business requires high adaptability of their manufacturing and automation equipment to adhere to the ever changing demand of their customers. Different manufacturing jobs have to be set up regularly with a high degree of safety, quality and speed. One misstep in any of those areas can have substantial consequences for Port Erie Plastic’s business. Mike, Automation Engineer for Port Erie Plastics, knew these challenges well and was always looking for ways to improve his job changeover process.
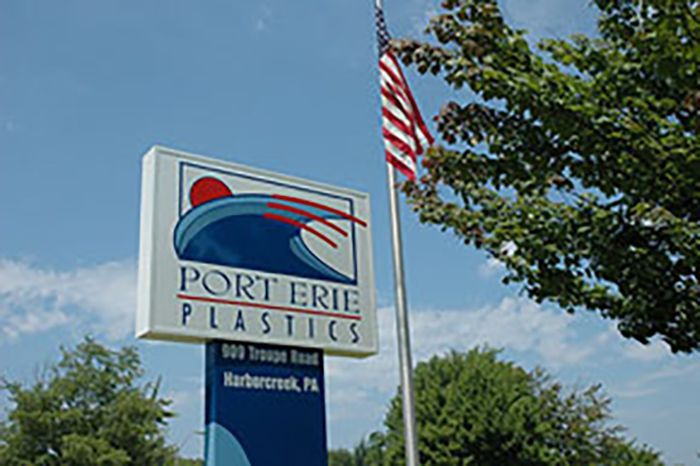
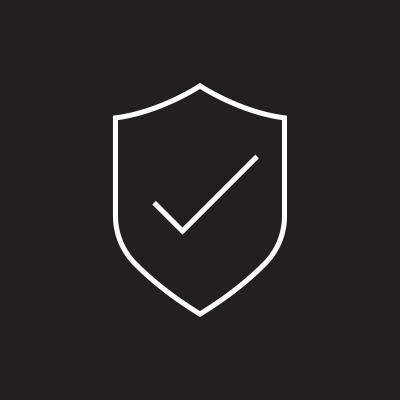
Safety
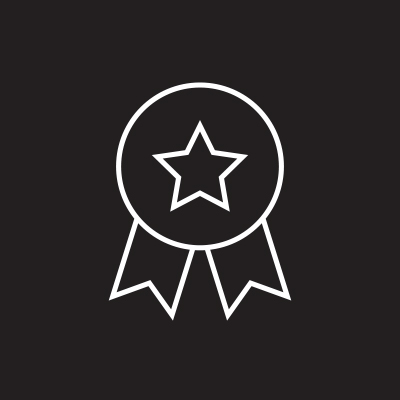
Quality
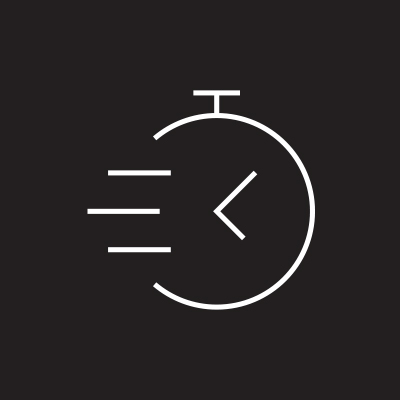
Speed
COVID-19 Essential Workplace
No better scenario displayed the need for adaptability than a recent highly critical job that came across Mike’s desk. In 2021, Port Erie Plastics was deemed an essential workplace due in part to a set of products for customers involved with responding to the Covid-19 outbreak. One particular customer had several molds that were running around the clock trying to meet demand. The customer required Port Erie to have new molds built with increased production capabilities. Port Erie Plastics Tool Room was awarded the work and the new molds were designed and built.
Mike was now tasked with redeploying the Universal Robot (UR) which was running a 2-cavity mold onto the new 4-cavity mold workcell. One of the biggest hurdles with robot redeployment is the need to accurately set moves and waypoints relative to how the robot was originally programmed. Mike knew based on the size of his program, touching up each waypoint and move could take days. He needed a quick way to be able to offset these moves and waypoints so the robot could quickly execute the job.
Luckily both of Mike’s 2-cavity and 4-cavity machines along with his Universal Robots were equipped with Flexxbotic’s Flexx Reference solution coupled with mobile carts based on the advice from Ben Mintz, Key Account Manager for Neff Automation. The Flexx Reference is a mechanical and software solution to program a Universal Robot relative to a reference point in a work cell. Ben who has worked on multiple projects with the Flexx Reference had this to say “The Flexx Reference coupled with a mobile cart allows any Universal Robot to easily and efficiently be repurposed anywhere on a manufacturing floor. It made perfect sense for Mike to integrate this kind of setup for his site.”

FlexxReference™ Execution
Mike had developed both work cells with the FlexxReference™ to help initial alignments as well as periodic adjustments, but now he needed to perform a full redeployment. The new 4-cavity mold was almost ready to be released from the tool room, and discussions turned to moving the robot and work cell to a new location. Because of the experience Mike had utilizing the FlexxReference™, he was able to respond to questions regarding the timing with a high degree of confidence that it would only be a matter of hours to shut down, move, and reinstall the cell rather than days.
He worked with the set-up crew including Brandon, Automation Engineer, to execute the redeployment. He allowed them time to pull the current mold from the new location that was running and then had them set up the new mold. Brandon and the automation team were now ready to begin the redeployment of the Universal Robot.
He unhooked it from the current station and rolled it up to the new station. He locked the robot wheels in place, captured the offset by locking the FlexxReference™ mechanical hardware together and saving the point in the URCap toolbar. The program’s waypoints and moves were successfully updated relative to the new reference point and Brandon finished up the redeployment with some end of arm tooling/tool center point changes. The redeployment took under an hour with the offset from the FlexxReference™ taking only 5 minutes. The redeployment and the job was a success as the heats were coming up on the press.
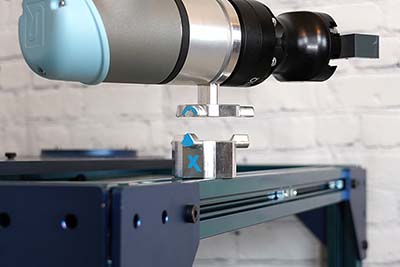
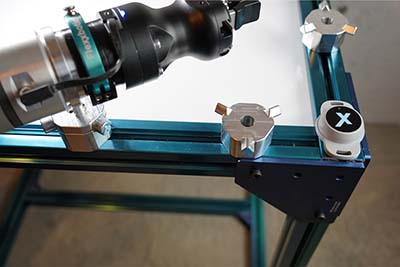
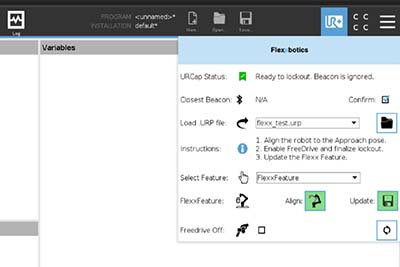
FlexxReference™ Benefits
At the end of the day, Mike said the “FlexxReference™ provided four core benefits to us:
1. Gave us reassurance the machine would be up and running once demand arrived
2. Reduced our engineering wages from 8 hours to 5 minutes when offsetting our robot moves and waypoints
3. Allowed me to delegate the redeployment so I could focus on other projects
4. Enabled us to time splice Universal Robots on our floor ultimately rethinking how we can justify new automation investment.”
Mike went on to further state “FlexxReference™ gave me the peace of mind to tell the facility confidently that I could get the Universal Robot up and running in less than 30 minutes.” With how successful the redeployment went, Mike has his eyes on new ways to utilize their Universal Robots. He plans to redeploy more frequently as his setup time to job time ratio justifies the redeployment easily.
To learn more about how the Flexx Reference could optimize your Universal Robot workflow, email us at info@flexxbotics.com